In this article we delve into alloys such as Inconel and Waspaloy, trying to better understand what their characteristics are and why they can be classified as superalloys.
In a previous article we made a classification of the various types of alloys used in aerospace, click here to read it again. Today we go into more detail and try to understand what the differences and characteristics of Inconel and Waspaloy are.
Superleague INCONEL
Inconel belongs to a family of nickel-based metal alloys, often referred to as “superalloys.” These alloys also contain chromium and iron, in addition to nickel.
To further enhance their properties, other alloying elements, such as molybdenum, tungsten and niobium, may also be present.
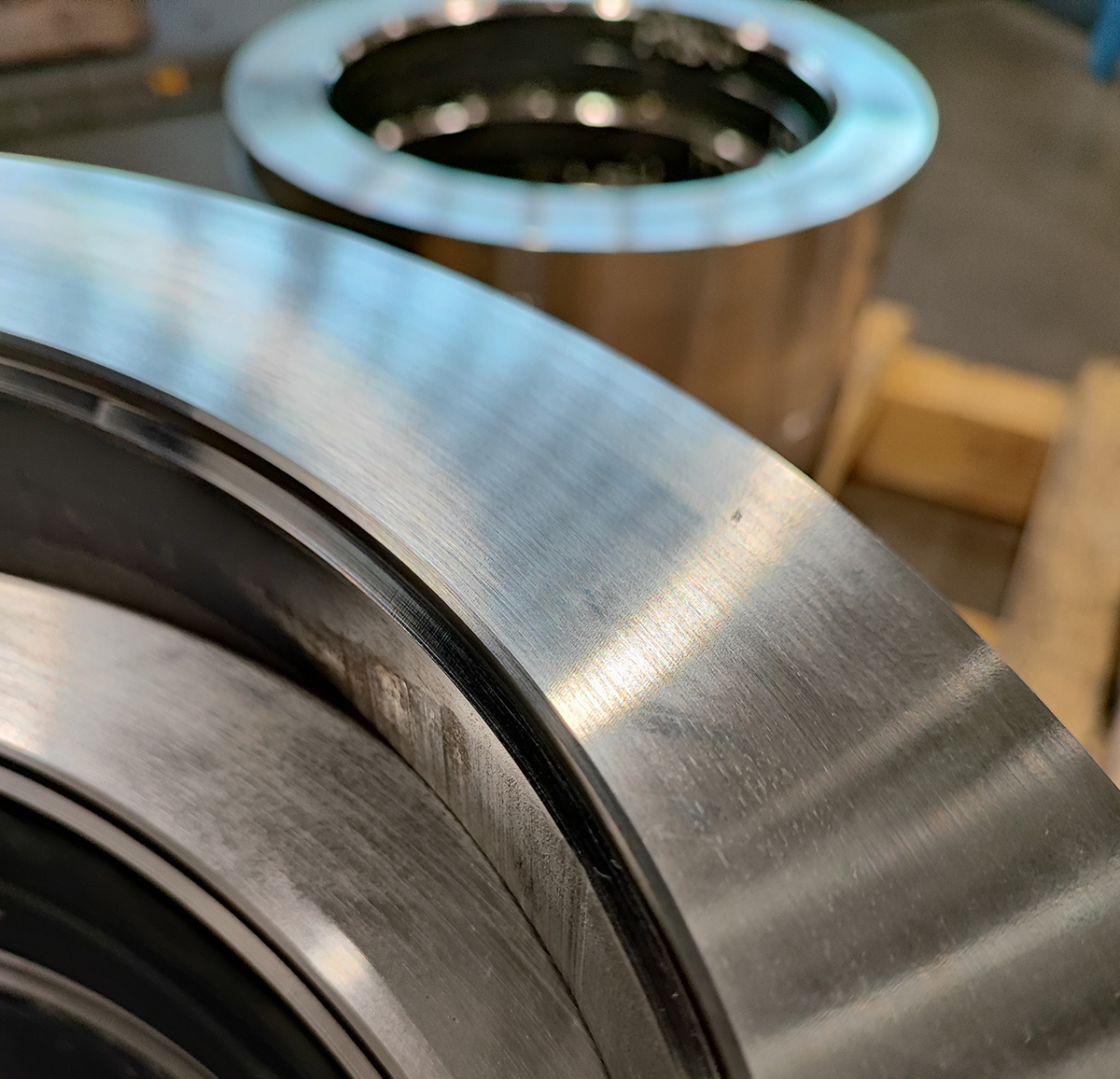
It is an ideal material for use in extreme environments, i.e., in applications characterized by high temperatures where aluminum and steel would be subject to wear. For this reason, inconel is particularly suitable for the manufacture of turbojet/ turboprop engine components.
However, although Inconel is particularly suitable for the manufacture of aircraft engine components, the aerospace industry is not the only sector in which this material currently finds application.
Heavy industry, where structures are usually exposed to extreme environments, is also a field that benefits from the characteristics of superalloy.
Gas turbine components, device components, power and process parts, ducts, valves and heat exchangers are just some of the possible applications of Inconel.
The Inconel series includes several alloys. Some of the most common include:
- Inconel 600
- Inconel 625
- Inconel 718
Each alloy has specific properties that make it suitable for certain applications.
Inconel alloys are renowned for their reliability and durability in extreme environments and are extensively researched and developed to improve their performance in various industrial settings.
Superalloy WASPALOY
Waspaloy is a nickel-based superalloy with high mechanical performance and high temperature resistance.
It is particularly known for its ability to maintain strength and hardness even at temperatures above 650°C (1,200°F). This makes it an ideal material for high-temperature and high-pressure applications.
Waspaloy has significant tensile strength and fatigue strength at elevated temperatures. This mechanical strength makes it suitable for applications where the material is subjected to significant mechanical loads.
Corrosion resistance is also good, especially in oxidizing environments and at high temperatures, making it useful in applications where a combination of mechanical strength and corrosion resistance is required.
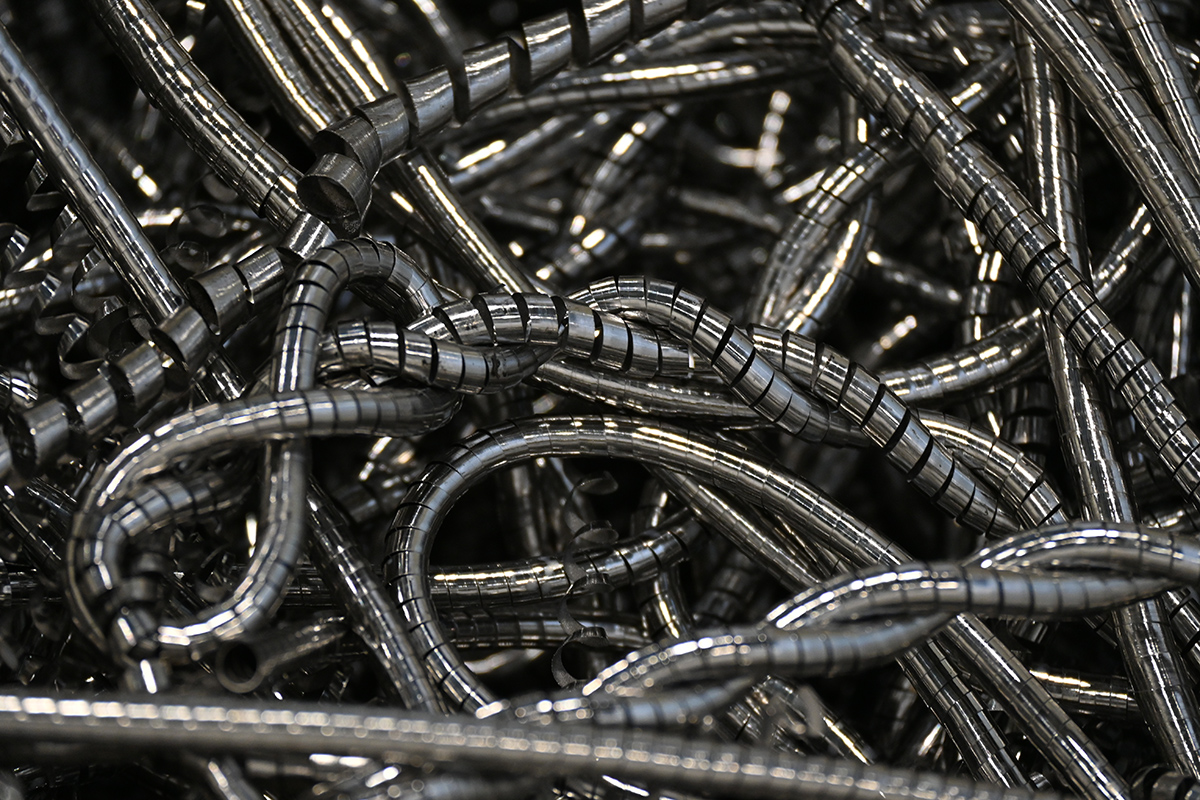
Waspaloy also retains its dimensional stability at elevated temperatures, making it suitable for applications where consistent dimensional accuracy is needed, such as aircraft engine parts, exhaust system components, and other critical parts of engines and gas turbines.
Waspaloy machining can be complex because of its mechanical and thermal properties. It is important to use high-quality cutting tools and follow specific machining procedures to achieve optimal results.
Inconel Vs Waspaloy: specificity
Both alloys therefore exhibit considerable corrosion resistance, but Inconel is known for its exceptional resistance to corrosive and aggressive environments, making it suitable for a wide range of applications where corrosion is a concern.
Waspaloy also offers good corrosion resistance, however, it is better suited to withstand extremely high temperatures under mechanical loading.
For more information about Lomec Aerospace’s services, contact us.