Evolution has been a constant for the entire aerospace industry since its inception.
An evolution that is never an end in itself, but essential to meet the increasingly stringent requirements imposed by the outside world. The goal today is to create increasingly efficient and fuel-efficient vehicles to limit environmental impact as well as costs.
This evolutionary process represents a challenge of increasing proportions for manufacturers of metallic materials used in aerospace applications.
Take jet engines as an example, which operate in extremely hostile environments characterized by high temperatures, the presence of corrosive agents, centrifugal forces, friction, high pressures and intense fatigue cycles.
Or think of structural components, such as aircraft cabin, landing gear, or fastening rivets, which are required to perform unparalleled well under conditions characterized by sudden temperature changes and prolonged stress.
All this ensures not only great efficiency, but also maximum reliability and operational safety.
To meet requirements of this magnitude, it becomes essential to be able to rely on specially designed high-performance materials, metal alloys and special alloys .
Such materials must therefore:
- Demonstrate extraordinary resistance to high temperatures
- Have the ability to resist corrosion and oxidation
- To offer an outstanding ratio of specific weight to mechanical strength
- boast great durability.
Classification of metal alloys and special alloys for aerospace
Depending on the type of application, different types of metal alloys and special alloys are used in aerospace, but each must be able to meet specific strength, weight and durability requirements.
Here are some of the most commonly used metal alloys:
Titanium
Titanium is known for its strength and lightness. Titanium alloys such as Ti-6Al-4V are commonly used in critical components, such as engine parts and aircraft structural parts.
Stainless steel
Stainless steels are often used for aircraft parts exposed to the elements or for those components that require superior corrosion resistance, such as in engines.
Magnesium alloys
Magnesium alloys are light but strong and are used in nonstructural parts and other aircraft components.
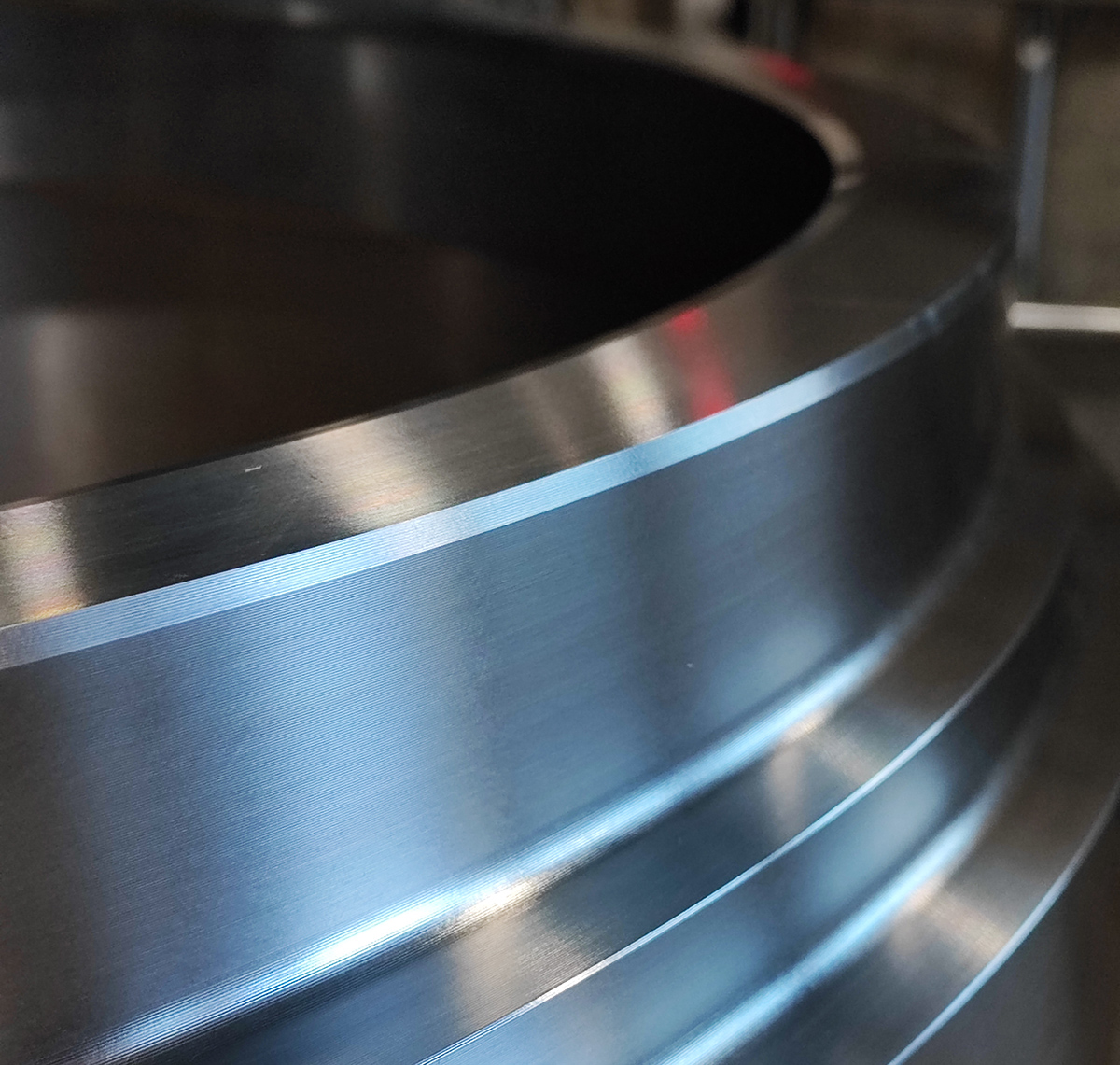
Composites
Although they are not metal alloys, composite materials are widely used in aerospace. They combine materials such as carbon fiber and resins to create lightweight and strong components.
Advanced materials
The aerospace industry continues to develop and adopt new advanced materials, such as shape memory metal alloys, nanocomposites and advanced composite materials, to improve aircraft performance and durability.
Aluminum
Aluminum alloys are widely used in many aircraft parts because of their light weight and corrosion resistance. Alloy 7075 is known for its high strength and is often used for structural parts.
Superalloys
These special alloys are designed to withstand extreme temperatures and high mechanical stresses. Some examples of such materials are nickel-based alloys such as Hastelloy and Waspaloy.
Inconel
Inconel is another material belonging to the nickel-based superalloy family that is remarkably resistant to high temperatures, corrosion, and oxidation.
These alloys, in addition to nickel, precisely, also contain chromium and iron and, in some cases, other alloying elements such as molybdenum, tungsten and niobium, which further enhance their properties.
Inconel alloys are widely used in the aerospace industry and other high-temperature and corrosion applications, such as aircraft engine parts, for example, compressor blades.
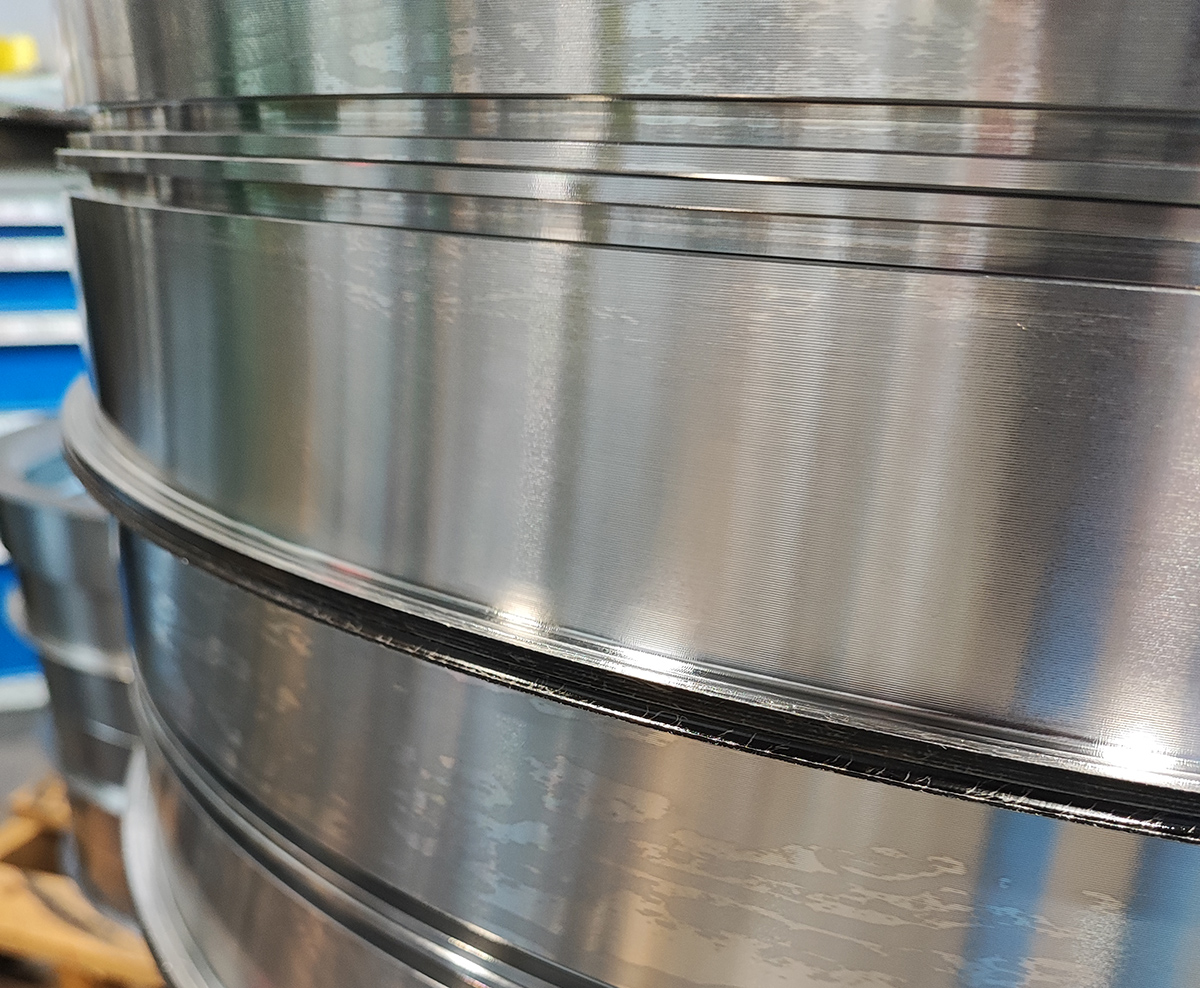
Why are aerospace alloys difficult to machine?
The special and exceptional characteristics that distinguish the metal alloys used in aerospace are also somewhat of a limitation for these materials in terms of workability.
That is why companies operating in the sector must necessarily rely on a specialized partner such as Lomec, which can process metal alloys and special aerospace alloys without compromising their properties.
The machining of Inconel, for example, represents one of the most onerous and difficult challenges a machine shop can face because of the material’s particular characteristics and how they affect its processing.
For example:
High hardness and strength
Inconel is known for its high hardness and strength, especially at high temperatures. This makes its mechanical processing difficult and requires the use of dedicated, particularly strong, high-quality tools and equipment.
Tendency to cold hardening
Inconel tends to harden during cold processing, gradually increasing the difficulty of the operation. This requires careful control of processing temperatures and may necessitate intermediate heating procedures in order to soften the material.
Tool wear and tear
Because of its hardness, Inconel can cause significant wear and tear on cutting tools and processing equipment, thus necessitating their frequent replacement, from which additional costs result.
Very low thermal conductivity
Inconel has very low thermal conductivity, which means that heat generated during machining tends to build up in the cutting zone. This can lead to problems of overheating, warping and tool deterioration.
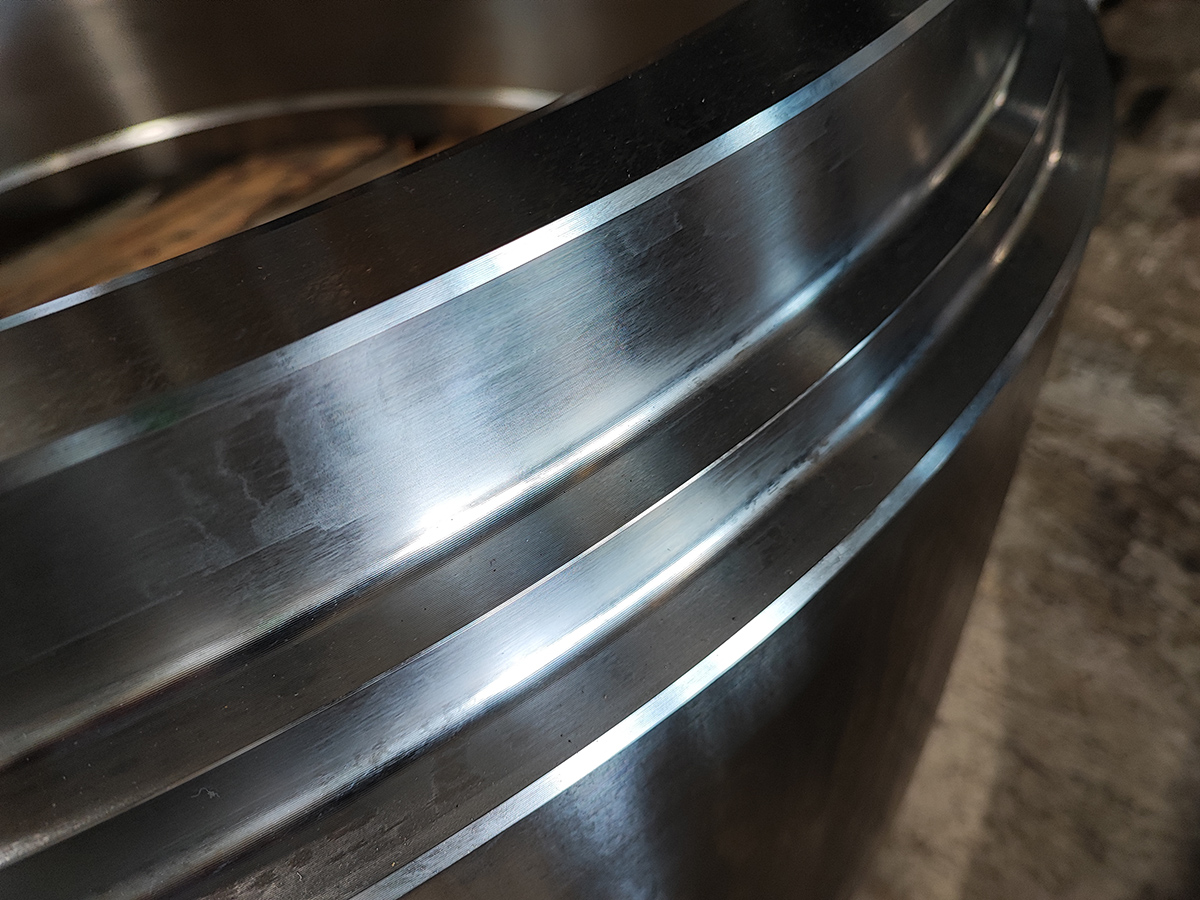
Tendency for machine hardening
Inconel processing can cause deterioration of the machines used due to the high pressures and loads applied. This may require more frequent maintenance of the machines.
Tight tolerances and surface finishes
Inconel machining often requires tight tolerances and precise surface finishes, which are difficult to achieve because of its material properties.
To meet these challenges, Lomec uses high-quality cutting tools designed specifically for Inconel processing.
Processing that in the company is entrusted to a team of experienced operators who specialize in handling this particular material, applying special cooling and lubrication techniques to prevent overheating and achieve the highest quality finished product possible.
Contact us for more information.